Acuity fast-tracks product development for makeshift hospitals
Necessity being the mother of invention means it can also speed up the emergence of useful things, as Acuity Brands has demonstrated by taking less than two weeks to design, manufacture, and ship a rugged light stand headed to makeshift centers being used to treat COVID-19 patients.
Atlanta-based Acuity is outfitting the new Portable Healthcare Light Stand with existing all-in-one exam, task, and night lights, including the Lithonia Lighting I-BEAM for exam purposes and the Lithonia OVFL for tasks. It is delivering 30 units to an alternate care site in Michigan today, an Acuity spokesperson told LEDs Magazine. Shipments to other locations are expected to follow shortly.
The stand and light package is one of many products that Acuity is making available on a rapid response basis to alternate care sites — non-traditional environments such as hotels and arenas being converted for medical purposes as defined by the US Army Corps of Engineers and the US Department of Health and Human Services.
The idea for the stand originated in text message exchanges between three Acuity associates on a Sunday roughly two weeks ago. After several product sketches, Acuity vice president of design engineering Ron Schimmelpfenning modified the design based on portable engine hoist stands, and built a prototype in about two days. Schimmelpfenning is a motorsports enthusiast.
The stand is designed so that the end user can unpack and assemble it in less than 5 minutes without specialized labor.
“Our Portable Healthcare Light Stand went from concept-to-completed design to first customer installation in less than two weeks,” said Steve Lydecker, Acuity senior vice president of applied technology solutions. Prior to today, Acuity had installed one of the light stands at an undisclosed location.
Normally, a new product would take at least several months to gestate, but Acuity found ways to expedite the process.
“Often in developing a product, there is a large committee involved,” the spokesperson explained to LEDs. “Due to the urgent need from alternative healthcare sites, we streamlined the process by cutting the committees. Additionally, we cut our normal business case approval process, lengthy market research, and price modeling exercises. Instead, we looked at the news, the US Army Corps of Engineers performance work statements, and tried to make some logical assumptions.”
The spokesperson described pricing as “minimal margin,” set at a level to cover the company’s costs and to “limit the cost burden to tax payers.”
Acuity is making the stands in Minnesota, and is prepared to also make them at sites in Illinois, Indiana, Georgia, Texas, and California, as needed.
“We hope that demand doesn’t grow as that would mean that more folks were in need of acute care,” the spokesperson said.
“We are getting new inquiries daily,” she noted. “Our teams are working very quickly to procure raw materials and schedule production to meet very aggressive delivery dates.”
The stand is intended for use in both acute and non-acute care spaces such as nurse stations, medication rooms, and corridors, as well as in certain patient pods.
The product development acceleration echoes the actions of British vertical farm specialist LettUs Grow, which this month fast-tracked two new growing areas in Bristol, England.
In a similar move, Kenosha, WI-based Kenall earlier this month introduced its KRT Series of luminaires that deliver general illumination as well as 405-nm light that kills certain bacteria. The company is making the line available on a fast-track basis to temporary hospitals.
Niles, IL-based A.L.P. Lighting Components has retooled production at a Michigan factory in order to manufacture a face shield it has designed to sell as personal protection equipment in the health field, as has an Iowa-based lighting company called Fire Farm Lighting, which is also putting into production a protective intubation enclosure design.
Meanwhile, the National Association of Electronics Manufacturers (NEMA) in the US has asked that the government deem lighting as a critical industry.
The moves comes as the lighting companies, like industry in general, figure out how to survive during the coronavirus pandemic. Rays of business recovery have emerged recently, as Signify has reopened plants in China, and Brussels-based Schréder Group has reopened certain European factories while also keeping open plants in China and Australia.
But the pandemic is taking its financial toll. The world’s two largest lighting companies, Signify and Osram have both pulled their forecasts for the year. Signify executives have taken a 20% pay cut and have asked employees to voluntarily reduce their pay and workload by 20%. Osram is considering asking employees to work less and has slowed production at a number of locations.
Signify and Lumileds have also raised prices, while Signify has already declined to participate in Frankfurt’s rescheduled Light + Building exhibition, which organizers had already moved from March to September because of the pandemic.
MARK HALPER is a contributing editor for LEDs Magazine, and an energy, technology, and business journalist ([email protected]).
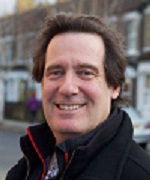
Mark Halper | Contributing Editor, LEDs Magazine, and Business/Energy/Technology Journalist
Mark Halper is a freelance business, technology, and science journalist who covers everything from media moguls to subatomic particles. Halper has written from locations around the world for TIME Magazine, Fortune, Forbes, the New York Times, the Financial Times, the Guardian, CBS, Wired, and many others. A US citizen living in Britain, he cut his journalism teeth cutting and pasting copy for an English-language daily newspaper in Mexico City. Halper has a BA in history from Cornell University.